Wie misst man die Bearbeitungsgenauigkeit von Maschinenteilen?
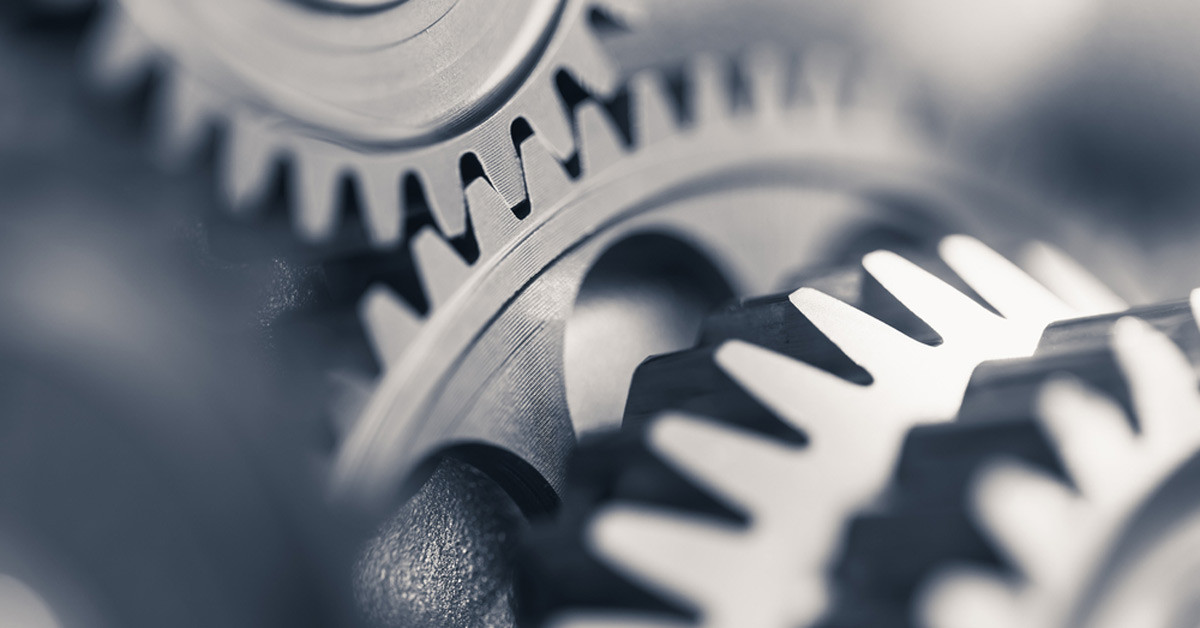
Die Bearbeitungsgenauigkeit ist der Grad der Übereinstimmung zwischen der tatsächlichen Größe, Form und Position der drei geometrischen Parameter der Oberfläche des bearbeiteten Maschinenteils und den von der Zeichnung geforderten idealen geometrischen Parametern. Die Verarbeitungsgenauigkeit nimmt unterschiedliche Messmethoden entsprechend den unterschiedlichen Verarbeitungsgenauigkeitsinhalten und Genauigkeitsanforderungen an. Generell gibt es folgende Arten von Methoden:
Direkte Messung und indirekte Messung
Je nachdem, ob der gemessene Parameter direkt gemessen wird, kann er in direkte Messung und indirekte Messung unterteilt werden.
Direkte Messung: Messen Sie den gemessenen Parameter direkt, um die gemessene Größe zu erhalten. Verwenden Sie zum Messen beispielsweise Messschieber und Komparatoren. Indirekte Messung: Messen Sie die geometrischen Parameter in Bezug auf die gemessene Größe und erhalten Sie die gemessene Größe durch Berechnung.
Offensichtlich ist die direkte Messung intuitiver und die indirekte Messung umständlicher. Wenn die gemessene Größe oder direkte Messung die Genauigkeitsanforderungen nicht erfüllt, muss im Allgemeinen eine indirekte Messung verwendet werden.
Absolute Messung und relative Messung
Je nachdem, ob der Lesewert des Messwerkzeugs direkt den Wert der gemessenen Größe darstellt, kann er in absolute Messung und relative Messung unterteilt werden.
Absolutmaß: Der abgelesene Wert gibt direkt die Größe der gemessenen Größe an, wie z. B. das Messen mit einem Messschieber.
Relativmessung: Der Ablesewert gibt nur die Abweichung der gemessenen Größe von der Normmenge an. Wenn Sie einen Komparator verwenden, um den Durchmesser der Welle zu messen, müssen Sie zuerst die Nullposition des Instruments mit einem Endmaß einstellen und dann die Messung durchführen. Der gemessene Wert ist die Differenz zwischen dem Durchmesser der Seitenwelle und der Größe des Endmaßes. Dies ist eine relative Messung. Im Allgemeinen ist die relative Messgenauigkeit höher, aber die Messung ist mühsamer.
Kontaktmessung und berührungslose Messung
Je nachdem, ob die gemessene Oberfläche Kontakt mit dem Messkopf des Messgeräts hat, wird sie in Kontaktmessung und berührungslose Messung unterteilt.
Kontaktmessung: Der Messkopf hat Kontakt mit der zu berührenden Oberfläche und es wirkt eine maschinelle Messkraft. Wie das Messen von Maschinengrundteilen mit einem Mikrometer.
Berührungslose Messung: Der Messkopf berührt nicht die Oberfläche des Messteils. Durch die berührungslose Messung kann der Einfluss der Messkraft auf das Messergebnis vermieden werden. Wie die Verwendung des Projektionsverfahrens, der Lichtwelleninterferometrie und so weiter.
Einzelmessung und Gesamtmessung
Entsprechend der Anzahl der Messparameter wird es in Einzelmessung und umfassende Messung unterteilt.
Einzelmessung: Jeder Parameter der getesteten Maschinenteile wird separat gemessen.
Umfassende Messung: Messen Sie den umfassenden Index, der die relevanten Parameter von Maschinenteilen widerspiegelt. Beispielsweise können beim Messen des Gewindes mit einem Werkzeugmikroskop der tatsächliche Steigungsdurchmesser des Gewindes, der Halbwinkelfehler des Zahnprofils und der kumulative Fehler der Gewindesteigung separat gemessen werden.
Eine umfassende Messung ist im Allgemeinen effizienter und zuverlässiger, um die Austauschbarkeit wertvoller Maschinenteile sicherzustellen, und wird häufig zur Inspektion fertiger Teile verwendet. Eine einzelne Messung kann den Fehler jedes Parameters separat bestimmen und wird im Allgemeinen zur Prozessanalyse, Prozessinspektion und Messung bestimmter Parameter verwendet.
Aktive Messung und passive Messung
Entsprechend der Rolle der Messung im Verarbeitungsprozess wird sie in aktive Messung und passive Messung unterteilt.
Aktive Messung: Das Werkstück wird während der Bearbeitung gemessen und das Ergebnis direkt zur Steuerung der Bearbeitung des Teils verwendet, um die Entstehung von Ausschuss rechtzeitig zu verhindern.
Passive Messung: Die Messung, die nach der Bearbeitung des Werkstücks durchgeführt wird. Diese Art der Messung kann nur beurteilen, ob das verarbeitete Teil qualifiziert ist, und beschränkt sich auf das Auffinden und Aussortieren von Abfallprodukten.
Statische Messung und dynamische Messung
Je nach Zustand des gemessenen Teils im Messprozess wird es in statische Messung und dynamische Messung unterteilt
Statische Messung: Die Messung ist relativ statisch. Wie ein Mikrometer, um den Durchmesser zu messen.
Dynamische Messung: Die gemessene Oberfläche und der Messkopf bewegen sich im simulierten Arbeitszustand während der Messung relativ zueinander.
Das dynamische Messverfahren kann den Zustand der Maschinenteile nahe am Gebrauchszustand wiedergeben, was die Entwicklungsrichtung der Messtechnik ist.
Die Bearbeitungsgenauigkeit von Maschinengrundteilen bestimmt direkt die Qualität der Teile und wirkt sich auch auf die Qualität der Maschinen aus. Wenn Sie nach dem Lesen des obigen Inhalts mehr über Maschinenteile und Lösungen erfahren möchten, können Sie es erhalten, indem Sie uns kontaktieren.
Als professioneller Teilelieferant verfügen wir über fortschrittliche Verarbeitungsgeräte und eine strenge Gewichtsprüfung, die Kunden hochpräzise verarbeitete Teile liefern kann. Und wir bieten auch einen durchdachten One-Stop-Service, der sich verpflichtet hat, Kunden gute Lösungen zu bieten. Wenn Sie unsere hochwertigen Maschinenteile kaufen möchten, kontaktieren Sie uns bitte umgehend!